Ok folks... time to add a new update to my build. I've been getting alot of questions about my new corridor sconce light sets on Shapeways. I made them because all the offerings so far (PE/SW) have all been too large! You should be able to fit 5 lights per large cushion. All the offerings so far you can only fit 3-4. That don't cut it for my OCD!
They both (the ESB and ANH versions) come with this little tool I designed called the Drill Guide.
But yet, no one can figure out how to use it. I painted it with primer so it's easy to see... It's really simple to use... here's how:
First things first, identify the top of each cushion that needs a light on it. On the back mark the top position so you don't forget. Then, take the edge of my tool and place it on the top edge as shown and push it against the surface of the cushion. Rub it back and forth creating a very light mark on the plastic (not so hard it does damage, and not so light you can't see it). You can prepaint the cushion whatever color you want and it'll make the marking a bit easier as well...
Next, dip the pointed marker ends in a little bit of paint (doesn't really matter what kind, I like to use watercolor or arcylic paint here because it can be removed easily if I make a mistake.
Next, touch the painted tips to the surface along the line you "rubbed" into the cushion previously. Just a dot of paint is all you need. These will be the drill points where you will drill a hole.
Some have worried about how it will work with the convex or concave cushions, well never fear, just by tilting it sideways you can still get a good point mark on those cushions easily as you can see below!
Convex Cushion:
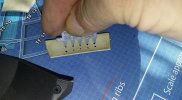
Concave Cushion:
You should now have perfectly spaced dots on each cushion. 5 for the large cushions (try to center them as best you can), 3-4 for the medium cushions and only 1 for the small ones. Now, you want to prepare your holes for drilling, so, take a sharp hobby knife and prep your drill holes. You don't want to make these too big, just large enough to give the drill bit something to grab onto as you start drilling your holes. Make the starter holes for each pin point marking you made earlier. Try to be as precise as possible in this step. If you move off the first line you made it'll show later.
Next you want to take a small drill bit (here I got a 1/16th) and begin drilling the holes in each cushion where you made your marking starter holes.
Now that you got all your small holes drilled, you have 2 options here. #1 you can begin gluing and drilling the large holes all the way thru both the cushion and the corridor parts or #2 you can set the part on the corridor and using the small holes drill thru the corridor. I chose the second option here because my larger drill isn't very delicate, so I have to be careful when I drill with it.
The drill bit to use for my corridor lights will be a 5/16th inch or 3.8mm bit.
Yes I know, an extra step! LOL
Now that all the holes are drilled you're ready to install the lights. Hope this helps and enjoy!
